When you open a file (that is not a media or an image file) from a container in 'non-mounted' mode, EDS decrypts the file to a temporary location on your device. Media files can be viewed directly from the container. In non-mounted mode you can open a container with FAT file system or ExFAT file system after installing an additional module. Download and Install EDS files from Rockwell's Website Step 1) If you don't get the option to upload the EDS file from the device when you right click on it, instead click on the Device Properties option: Step 2) Next, note the product information including the EDS file name so you can get the correct EDS file from the vendor.
Download the latest software and accessories from the SOFTWARE DOWNLOADS tab, or click on the REGISTRATION tab to request an activation code (register for use).
Contact KEYENCE for help downloading items marked with Available for Purchasers Only
SOFTWARE DOWNLOADS | REGISTRATION (ACTIVATION CODE GENERATION) |
XG-H1XA VisionEditor / VisionTerminal
This integrated development environment software allows users to configure and edit XG-X Series settings using a PC. Click here to activate (register for use). |
This software allows users to collect image data and results data from the controller on a PC easily and to display and manipulate controller screens on a PC. |
Offering only the simulation function of the VisionEditor software, this software can be used on multiple PCs with only one license. Click here to activate (register for use). |
Controller Firmware
This firmware is for use with XG-X Series controllers. |
CA-H1DB VisionDatabase
This database provides long-term storage of image and result data, and backups of inspection settings. A two week trial period is available after installation. Click here to activate (register for use). *A CA-H1DB license and CA-AD1 are required to use this product. |
XG-X ActiveX Control
This is an ActiveX control for creating a Windows application that operates the controller, and collects data or image output from the controller. |
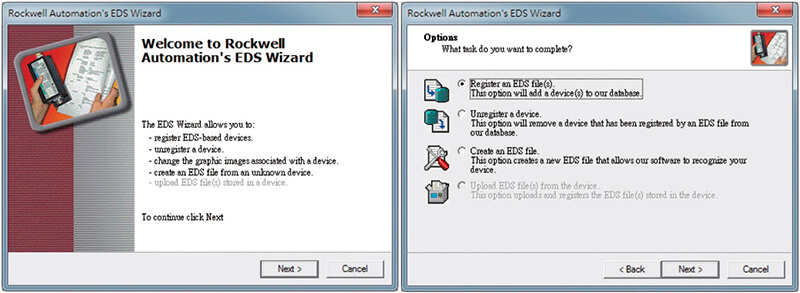
Communication Files
This driver is used for USB connection to a PC. |
These files are used for connecting XG-X Series products to a PLC via EtherNet/IP. Registration of these EDS files is not necessary for KEYENCE KV Series products. If XG-X Series cannot be selected in your version of KV STUDIO, please update to the latest version of KV STUDIO. |
These files are used for connecting XG-X Series products to a PLC via CC-Link. |
These files are used for connecting XG-X Series products to a PLC via PROFINET. |
These files are used for connecting XG-X Series products to a PLC via EtherCAT. |
XR Software (For PC connection type XR 3D cameras)
This firmware is for use with PC connection type XR 3D cameras. |
The software allows users to connect to, configure, and view images from PC connection type XR-HTMD 3D cameras. |
REGISTRATION (ACTIVATION CODE GENERATION)
Activation is required for the XG-X VisionEditor and XG-X Simulator+ Software. Once logged in to your Keyence.com account, you can request an activation code for the software you need at the links below. For XG-X Vision Editor, note that you can apply for a full activation code if you have a purchased license, or you can apply for a one-time 30-day trial code. During business hours, you can expect a code to be sent to your registered account e-mail within 30 minutes.
At the bottom of this page, you can find activation code request links for the XR-HT GigE software. There are full license codes and 15-day trial codes available.
Note that e-mail addresses from free services, like Gmail or Hotmail, are not supported. Please update your account information or contact your KEYENCE sales representative if you need to add your company e-mail for registration.
XG-X Series
Activation codes for purchasers
Trial activation codes
XR Series
Activation codes for purchasers
Trial activation codes
This topic describes the concepts involved in setting up an EtherNet/IP I/O connection. For step-by-step procedures for Allen-Bradley, Omron, or Schneider Electric PLCs, see the Using Allen-Bradley Controllers via EtherNet/IP I/O, Using Omron Controllers via EtherNet/IP I/O, and Using Schneider Electric PLCs via EtherNet/IP I/O topics. For details on controlling the RMC once a connection has been made, see the Using an EtherNet/IP I/O Connection topic.
Setting up an EtherNet/IP I/O connection involves the following concepts:
Using the Correct EDS File
Electronic Data Sheet files (EDS files) are used by many vendors' EtherNet/IP configuration tools to help configure the communications. For configuration tools that do not use EDS files to configure EtherNet/IP I/O connections, see Using a Generic EDS below.
Several EDS files are available for the RMC controllers. EDS files are included when installing RMCTools to your computer. Current versions of EDS files are also available for download from Delta’s website www.deltamotion.com. Each EDS file is packaged in a compressed (.zip) file with its corresponding icon.
From the following table, choose the correct EDS file for your RMC and RMC firmware version:
Product | RMC Firmware | EDS File | Version1 | Download Location |
RMC75E | 2.20-3.40.x | rmc75e_v1.eds | 1.x | |
3.41.0-3.61.x | rmc75e_v2.eds | 2.1 | ||
3.62.0 or newer | rmc75e_v3.eds | 3.1 | ||
RMC150E | 2.20-3.40.x | rmc150e_v1.eds | 1.x | |
3.41.0-3.61.x | rmc150e_v2.eds | 2.1 | ||
3.62.0 or newer | rmc150e_v3.eds | 3.1 | ||
RMC200 CPU20L | 1.14.0 or newer | r200-cpu20L_v1.eds | 1.1 | |
RMC200 CPU40 | 1.06.0 or newer | r200-cpu40_v1.eds | 1.1 |
1This revision refers to the EtherNet/IP Identity Object revision, not the firmware revision. This revision only changes when the EtherNet/IP functionality is changed.
Once the correct EDS compressed file has been downloaded, extract the EDS file and icon to a temporary folder and import them into your EtherNet/IP configuration tool.
The correct EDS file is also embedded in the RMC controller itself and may be uploaded into the EtherNet/IP configuration tool, if supported by that particular tool. The steps required for this are tool-specific. Embedded EDS files are not supported by RMC75/150 firmware 3.40.x or older.
Connection Type
The RMC supports three types of I/O connections:
Input/Output
This connection is bidirectional: the originator (PLC or HMI) produces data consumed by the RMC and the target (RMC) produces data that is consumed by the originator. This connection type is also called an Exclusive Owner connection or the controlling connection.Input Only
For this connection type, only the target (RMC) produces data, which is consumed by the originator (PLC or HMI). The originator will only send a heartbeat packet, sometimes at a reduced interval (less frequently than the RPI) used to allow the RMC to identify when the connection is broken.Listen Only
This connection type is identical to an Input Only connection type, with one exception: a Listen Only connection can only exist when one of the other I/O connection types has been established. That is, a Listen Only connection cannot be established until an Input/Output or Input Only connection has been established, and conversely when the last non-Listen-Only connection has been closed or has timed out, the Listen Only connection will automatically close as well. This connection type is the least-frequently used. This connection type is not supported by RMC75/150 firmware 3.40.x or older.
Of these three, the Input/Output connection type is by far the most commonly used. The other two are generally only used when multiple I/O connections are used. See the Multiple EtherNet/IP I/O Connections topic for details.
Max Number of Connections and Data
Connection Type | RMC75E | RMC150E | RMC200 |
Total I/O Connections | 4 | 4 | 4 |
Input/Output Connections | 1 | 1 | up to 3 |
Input Only Connections | up to 4 | up to 4 | up to 4 |
Listen Only Connections | up to 4 | up to 4 | up to 4 |
Connection#1 Size | 125 input registers 124 output registers | 125 input registers 124 output registers | 360 input registers 360 output registers |
Connection#2 Size | n/a | n/a | 125 input registers 124 output registers |
Connection#3 Size | n/a | n/a | 125 input registers 124 output registers |
When using the RMC’s EDS file in your EtherNet/IP configuration tool, you should be able to select the I/O connection type from a list. Notice that in addition to the three listed above, you may also see Input/Output with Config and Input Only with Config. These connection types are generally not used. If you are using a Generic EDS File (as required by RSLogix 5000 prior to version 20), see the Using a Generic EDS File section below.
Since the RMC200 supports 3 I/O connections, it is possible for several PLCs to communicate with the RMC at once, each with a controlling connection. This is not possible to for the RMC75 and RMC150, as they support only one I/O connection.
Requested Packet Interval (RPI)
EtherNet/IP I/O sends data between the communicating devices at the Requested Packet Interval (RPI). The RPI is configured in the EtherNet/IP controller (for example, RSLogix 5000), not in RMCTools. The RMC supports the following RPIs, based on the number of simultaneous I/O connections established (see the Multiple EtherNet/IP I/O Connections topic):
I/O Connections | Minimum RPI | Minimum RPI | Minimum RPI | Typical RPI | Maximum RPI |
1 (typical) | 2 ms | 1ms* | 1ms | 20 ms | 10,000 ms |
2 | 3 ms | ||||
3 | 4 ms | ||||
4 | 4 ms |
*Not all CPU20L connections can be 1 ms. The CPU20L supports a bandwidth of 6000 packets per second and the CPU40 supports 8000 packets per second. The bandwidth of each connection is calculated as ( 2 / RPI ). For example, an RPI of 1 ms is 2/0.001 = 2000 packet/sec. The CPU20L can support 3 connections at 1 ms RPI.
The RPI must be both an integer number of milliseconds and a multiple of the RMC’s Loop Time. For example, an RPI of 9 ms would not be allowed for a loop time of 2 ms or 4 ms, but would be for 1 ms or lower loop times.
Delta recommends using the slowest RPI that meets the requirements of your application in order to reduce network requirements. See the EtherNet/IP I/O Performance topic for more details.
Multicast vs. Point-to-Point (Unicast)
The RMC supports both multicast and unicast (point-to-point) I/O connections. In almost all cases, unicast I/O connections should be selected whenever supported by the EtherNet/IP I/O controller, in order to reduce network traffic.
The RMC75/150 require multicast I/O connections only when multiple I/O connections will be established at once, which is quite rare. The RMC200 allows multiple unicast I/O connections.
Input Data
The Input Data is the data produced by the RMC and sent to the PLC. By default, the source of the Input Data is the Indirect Data Map, beginning with Indirect Data Map item 0. First, you must set up the Indirect Data Map in RMCTools to map to the RMC registers you want to transfer. Typically, you would include Actual Positions, Status and Error Bits for each axis of control, task status registers so the PLC can tell which user programs are running, and any other registers of your choice. The Input Data source can be changed to something other than the Indirect Data Map, as described below, but the Indirect Data Map is used in nearly all EtherNet/IP I/O applications.
The size of the Input Data is specified in the PLC when configuring the EtherNet/IP I/O connection. This should be set to the number of registers you have set up in the Indirect Data Map, plus the Sync Register, if used. For details on the Sync Register, see the Using an EtherNet/IP I/O Connection topic.

Once an EtherNet/IP I/O connection is established, the Input Data will automatically be sent from the RMC to the PLC each RPI. The PLC can use the data whenever it needs it.
Setting the Input Data Source in RMCTools
To set the source in the RMC for the Input Data:
In the Project pane, expand the Modules folder, double-click the CPU module, and choose EtherNet/IP.
Under I/O Connection Settings, in the Outgoing Data box, use the browse button to use the Address Selection Tool to find the location you want to use.
If using multiple connections, repeat for the other connections.
Notice that the length of the Input Data is specified in the PLC, not in RMCTools.
Output Data
The Output Data is the data sent from the PLC and consumed by the RMC. By default, the destination of the Output Data is the Indirect Data Map. This allows the PLC to easily write to whatever registers you have mapped into the Indirect Data Map, such as variables and axis command registers. The destination of the Output Data can be changed to something other than the Indirect Data Map registers, as described below. However, the Indirect Data Map works very well for most applications.
The size of the Output Data is specified in the PLC when configuring the EtherNet/IP I/O connection. The Output Data size must be the number of registers you wish to write, plus the Sync Register, if used. For details on the Sync Register, see the Using an EtherNet/IP I/O Connection topic.
Once an EtherNet/IP I/O connection is established, the Output Data is used to write to the RMC. Refer to the Using an EtherNet/IP I/O Connection topic for details.
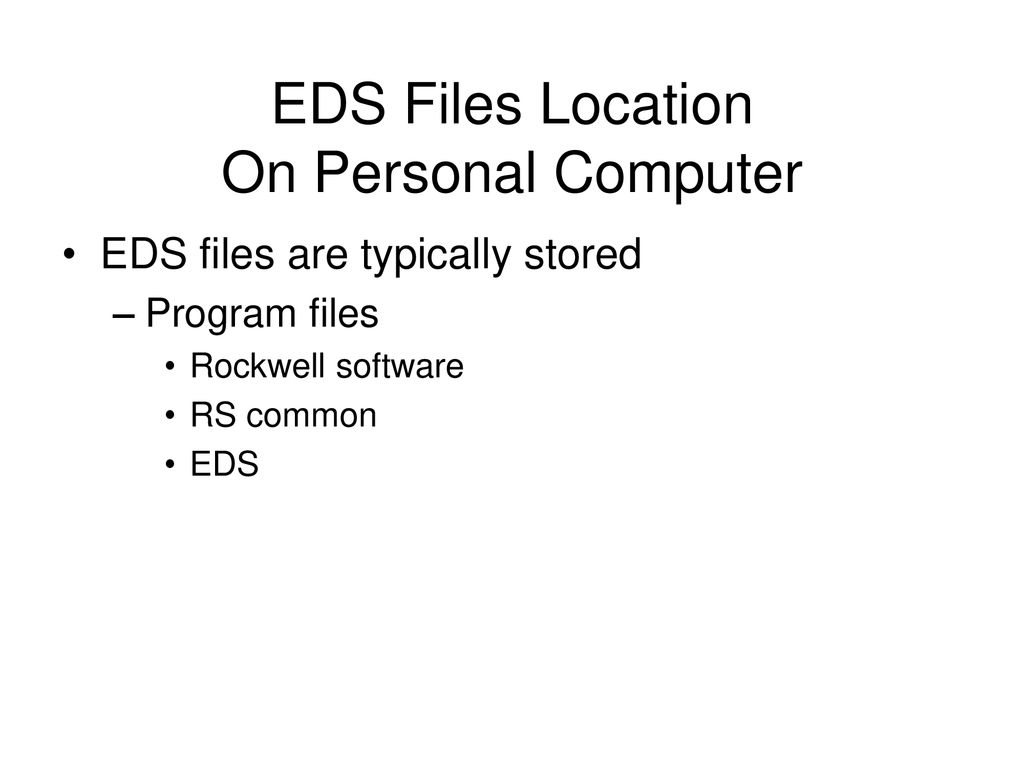
Setting the Output Data Destination in RMCTools
To set the destination in the RMC for the Output Data:
In the Project pane, expand the Modules folder, double-click the CPU module, and choose EtherNet/IP.
Under I/O Connection Settings, in the Incoming Data box, use the browse button to use the Address Selection Tool to find the location you want to use.
If using multiple connections, repeat for the other connections.
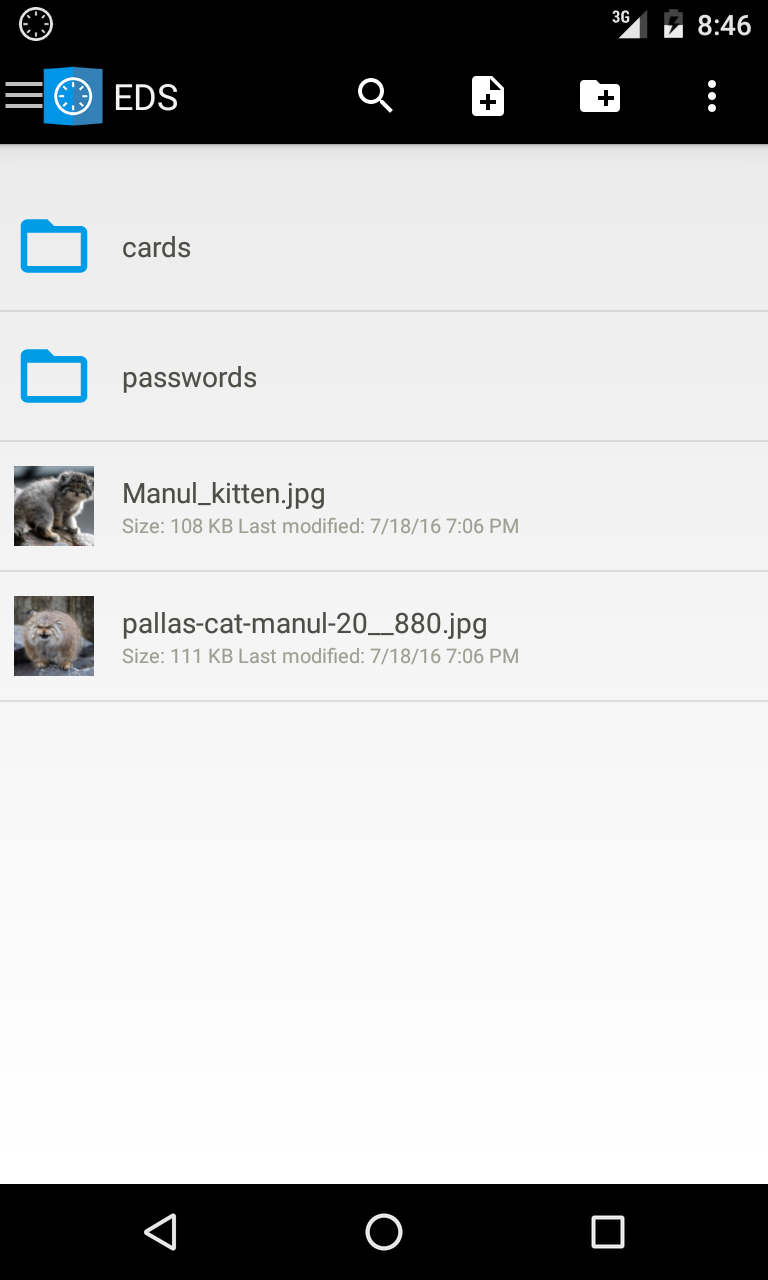
Notice that the length of the Output Data is specified in the PLC, not in RMCTools.
Eds Files Rockwell Download
Using a Generic EDS File
Eds Files
Some PLC EtherNet/IP configuration tools do not support importing third-party EDS files. In these cases, additional connection configuration information usually must be entered into a generic device template. The following charts provides the correct values for various connection settings that may be required by your EtherNet/IP configuration tool:
RMC75/150 Connections:
Setting | Connection Type | ||
Input/Output | Input Only | Listen Only | |
Input Connection Point1,2 | 1 | ||
Output Connection Point1,2 | 2 | 32 | 33 |
Config Data Assembly Instance2 | 4 | ||
Connection Path2 | 20 04 24 04 2C 02 2C 01 | 20 04 24 04 2C 20 2C 01 | 20 04 24 04 2C 21 2C 01 |
Transport Class | 13 | ||
Trigger Type | Cyclic3 | ||
O->T Format | 32-bit Run/Idle3 | Heartbeat | |
O->T Fixed/Variable | Fixed3 | ||
O->T Connection Type | Point-to-point3 | ||
O->T Priority | Scheduled3 | ||
O->T Size | 4, 8, …, 496 bytes | 0 bytes | |
T->O Format | Modeless3 | ||
T->O Fixed/Variable | Fixed3 | ||
T->O Connection Type | Point-to-point or Multicast | ||
T->O Priority | Scheduled3 | ||
T->O Size | 4, 8, …, 500 bytes | ||
O->T RPI | 2ms to 10000ms | ||
T->O RPI | 2ms to 10000ms | ||
Configuration Data Size | 0 bytes |
RMC200 Input/Output Connections:

Setting | Input/Output Connection #1 | Input/Output Connection #2 | Input/Output Connection #3 |
Input Connection Point1,2 | 1 | 5 | 7 |
Output Connection Point1,2 | 2 | 6 | 8 |
Config Data Assembly Instance2 | 4 | 4 | 4 |
Connection Path2 | 20 04 24 04 2C 02 2C 01 | 20 04 24 04 2C 06 2C 05 | 20 04 24 04 2C 08 2C 07 |
Transport Class | 13 | ||
Trigger Type | Cyclic3 | ||
O->T Format | 32-bit Run/Idle3 | ||
O->T Fixed/Variable | Fixed3 | ||
O->T Connection Type | Point-to-point3 | ||
O->T Priority | Scheduled3 | ||
O->T Size | 4, 8, …, 1440 bytes | 4, 8, …, 496 bytes | 4, 8, …, 496 bytes |
T->O Format | Modeless3 | ||
T->O Fixed/Variable | Fixed3 | ||
T->O Connection Type | Point-to-point or Multicast | ||
T->O Priority | Scheduled3 | ||
T->O Size | 4, 8, …, 1440 bytes | 4, 8, …, 500 bytes | 4, 8, …, 500 bytes |
O->T RPI | 1ms to 10000ms | ||
T->O RPI | 1ms to 10000ms | ||
Configuration Data Size | 0 bytes |
RMC200 Input Only Connections:
Setting | Input Only Connection #1 | Input Only Connection #2 | Input Only Connection #3 |
Input Connection Point1,2 | 1 | 5 | 7 |
Output Connection Point1,2 | 32 | 32 | 32 |
Config Data Assembly Instance2 | 4 | 4 | 4 |
Connection Path2 | 20 04 24 04 2C 20 2C 01 | 20 04 24 04 2C 20 2C 05 | 20 04 24 04 2C 20 2C 07 |
Transport Class | 13 | ||
Trigger Type | Cyclic3 | ||
O->T Format | Heartbeat | ||
O->T Fixed/Variable | Fixed3 | ||
O->T Connection Type | Point-to-point3 | ||
O->T Priority | Scheduled3 | ||
O->T Size | 0 bytes | ||
T->O Format | Modeless3 | ||
T->O Fixed/Variable | Fixed3 | ||
T->O Connection Type | Point-to-point or Multicast | ||
T->O Priority | Scheduled3 | ||
T->O Size | 4, 8, …, 1440 bytes | 4, 8, …, 500 bytes | 4, 8, …, 500 bytes |
O->T RPI | 1ms to 10000ms | ||
T->O RPI | 1ms to 10000ms | ||
Configuration Data Size | 0 bytes |
RMC200 Listen Only Connections:
Setting | Listen Only Connection #1 | Listen Only Connection #2 | Listen Only Connection #3 |
Input Connection Point1,2 | 1 | 5 | 7 |
Output Connection Point1,2 | 33 | 33 | 33 |
Config Data Assembly Instance2 | 4 | 4 | 4 |
Connection Path2 | 20 04 24 04 2C 21 2C 01 | 20 04 24 04 2C 21 2C 05 | 20 04 24 04 2C 21 2C 07 |
Transport Class | 13 | ||
Trigger Type | Cyclic3 | ||
O->T Format | Heartbeat | ||
O->T Fixed/Variable | Fixed3 | ||
O->T Connection Type | Point-to-point3 | ||
O->T Priority | Scheduled3 | ||
O->T Size | 0 bytes | ||
T->O Format | Modeless3 | ||
T->O Fixed/Variable | Fixed3 | ||
T->O Connection Type | Multicast | ||
T->O Priority | Scheduled3 | ||
T->O Size | 4, 8, …, 1440 bytes | 4, 8, …, 500 bytes | 4, 8, …, 500 bytes |
O->T RPI | 1ms to 10000ms | ||
T->O RPI | 1ms to 10000ms | ||
Configuration Data Size | 0 bytes |
1 The term ‘Assembly Instance’ is used by some applications instead of ‘Connection Point’.
2 The Input and Output Connection Points and Config Data Assembly Instance are implied by the Connection Path. Therefore, configuration tools will generally either ask for the Connection Points and Instances or the Connection Path but not both.
3 This value is the common default value for this setting and the option to change this field may not be offered by the configuration tool.
Unfortunately which fields are required and how they are presented varies significantly from one tool to the next. For this reason, most EtherNet/IP configuration tools are moving toward supporting importing EDS files to reduce the complexity of setting up an I/O connection.
Advanced Multicast Settings
In addition to the standard settings described above, the RMC provides advanced multicast I/O connection settings. These include the ability to override the default multicast address and Time To Live (TTL) value. See the EtherNet/IP Settings Page topic for details on these settings.
Eds Files Schneider
See Also
Eds Files For Rslinx
EtherNet/IP Overview | Using an EtherNet/IP I/O Connection | Using Allen-Bradley Controllers via EtherNet/IP I/O | Using Omron Controllers via EtherNet/IP I/O
Eds Files Studio 5000
Copyright (c) 2005-2020 by Delta Computer Systems, Inc.